Installation and Commissioning
Installation and Commissioning
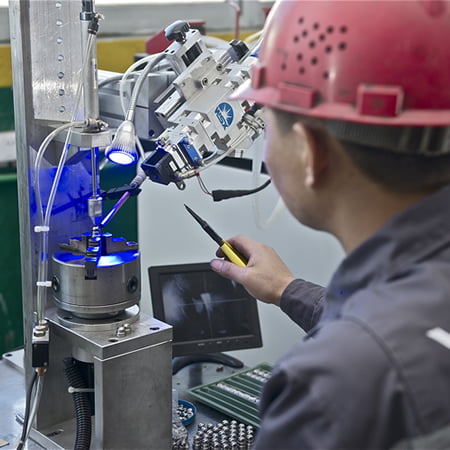
Valve Installation Method
Valve is a device that controls the flow of media. Generally, there are two installation methods: forward and reverse. Forward installation means that the flow direction of the valve is consistent with the flow direction of the medium, while reverse installation is the opposite. When forward installation, the closing pressure of the valve is small, which can speed up the closing speed, but it will affect the flow when throttling; reverse installation is the opposite of forward installation.

Inverted Installation Of Valves
Although the forward and reverse installation of valves has been widely used, inverted installation is also necessary in some special cases. For example, the installation space is too small, the flow direction of the medium in the pipeline is reversed, etc. However, it should be noted that there are some problems that need to be paid attention to when installing the valve inverted:
- The sealing performance of the valve will be reduced, and the closure will not be tight, which may easily lead to leakage.
- Inverted installation will cause the inlet end of the valve stem to be in the medium, which may easily cause pollution and reduce the life of the valve.
- The opening and closing method of the valve needs to be adjusted to prevent damage.
Precautions
The following points should be noted when installing the valve:
1. Clean the pipes before installation to make sure they are clean.
2. Choose the appropriate valve size and material.
3. During the installation process, follow the requirements in the valve manual.
4. After installation, strict trial operation and testing should be carried out to ensure the normal operation of the valve.
Valve Commissioning Method
Valve debugging usually requires the following four methods:
After the installation is completed, first conduct a manual operation test. Manually open and close the valve to check whether its operation is flexible and the indication is accurate. At the same time, observe whether there are any abnormal phenomena during the opening and closing of the valve.
After the manual operation test is correct, conduct a sealing test. Close the valve and observe whether there is leakage at the connection between the valve and the pipeline. If leakage is found, find the cause in time and take appropriate remedial measures.
On the basis of ensuring the good sealing of the valve, functional testing is carried out. According to the process flow of the system, the actual operating conditions are simulated to test whether the valve’s switching performance, adjustment performance, etc. meet the requirements.
If the valve is equipped with an automatic adjustment system, it is also necessary to debug the automatic adjustment system. According to the control requirements of the system, adjust the control parameters of the valve and test the accuracy and stability of the automatic adjustment system.
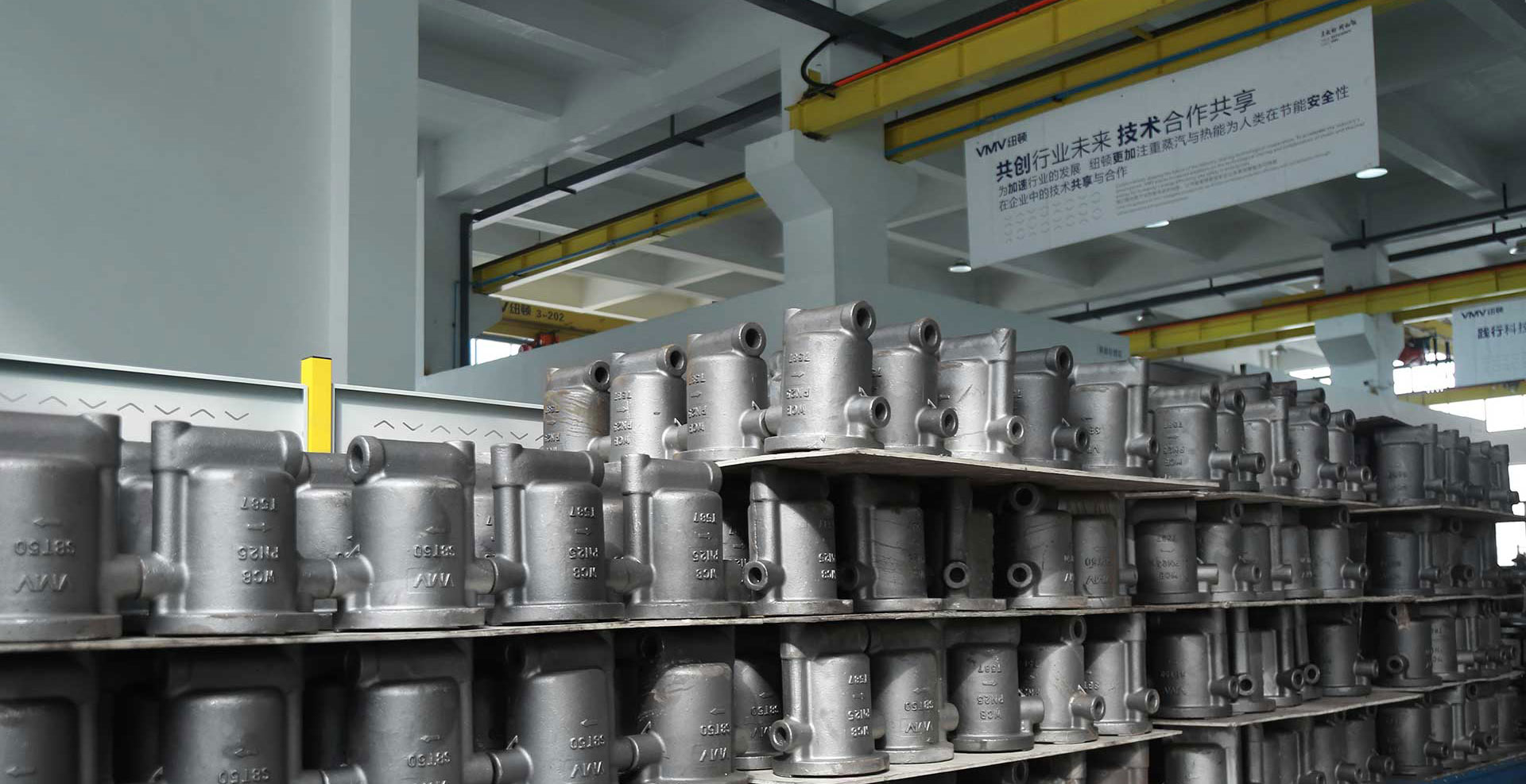